INTRODUCTION
Falling to the ground and rising up from a fall has emerged as a major challenge recently. As defined by the World Health Organization, a fall is an act of “inadvertently coming to rest on the ground, floor or other lower level, excluding intentional change in position to rest in furniture, wall, or other objects”. A fall can cause serious injuries such as bruises, broken bones, head and neck injuries, and/or emotional distress ( Alabdullgader and Rabbani, 2021). Annually, 684,000 individuals die from falls globally, which is considered the second largest cause of unintentional injury death. There are more than 37 million fall injuries that require medical care yearly ( World Health Organization, 2021). The Center for Disease Control and Prevention (CDC) of the United States of America anticipates seven fall deaths every hour by 2030 ( Bergen et al., 2016; CDC, 2022b). In Saudi Arabia, falls are the sixth major cause of death and the seventh major cause of living with a disability ( IHME, 2022).
Falling to the floor is associated with multiple risk factors such as (i) biological factors, which cannot be modified such as age, gender, race, and chronic diseases; (ii) behavioral factors, which focus on human actions, emotions, daily choices, drug interactions, and excess alcohol use; (iii) environmental factors, where most of the falls occurred indoors, due to poorly designed houses, poorly lighted rooms, and slippery floors such as the bathroom wherein most falls occur; and (iv) socioeconomic factors, such as living alone, low education, low salary, social isolation, restricted health care, and limitation of resources ( World Health Organization, 2021). In addition to the risk factors mentioned above, obesity can be considered as a risk factor that plays a role in all previously mentioned factors ( CDC, 2022a).
Given that seniors are a vulnerable segment of the society, obese seniors who have a body mass index (BMI) of ≥40 kg/m 2 face a greater risk of falling by 16% compared with nonobese seniors ( Neri et al., 2020; Alabdullgader and Rabbani, 2021). In a study by Cameron et al. on resident seniors in long-term health care facilities it was found that 56.2% of seniors fell at least once during a six-month time span ( Cameron et al., 2018). A study performed on 269 seniors found that 84.7% of the falls were indoors such as the washroom (27.8%), stairs (25%), and bedroom (16.7%) ( Alabdullgader and Rabbani, 2021). Occasionally there are falls which occur at the front doorstep (15.3%) or in the kitchen (12.5%). Outdoor falls were infrequent with only 15.3% ( Alabdullgader and Rabbani, 2021) of reported total falls.
With aging, falling can be considered as a risk factor, as well as the inability to rise up after a fall ( Bloch, 2012; Bergen et al., 2016; CDC, 2022b). 50% of the seniors face difficulties in rising up after falling to the ground and most of them stay laying on the floor for >1 h, which may increase the risk of pressure sores, pneumonia, and even death ( Swancutt et al., 2020). In a study conducted on 110 seniors, it was reported that 60% fell to the floor in which the majority fell at least twice ( Fleming et al., 2008). And among them 265 fall incidents were reported in which 54% were found on the floor. Of those who fell, 82% said that they were alone at the time of the fall. Furthermore, four out of every five people needed assistance getting up, and one-third remained on the floor for more than an hour ( Fleming et al., 2008). Those who remained on the floor for >2 h after a fall, faced an increased risk of dehydration, pressure ulcers, rhabdomyolysis, hypothermia, and pneumonia ( Rubenstein, 2006).
There are multiple techniques to reduce the risk of falls and help to stand after a fall. These techniques include devices that prevent from falling or assist after a fall. Some examples of these devices include, but are not limited to, a motion sensing device that follows postoperative senior patients in the hospital to ensure their safety from falling by catching the patient and preventing their fall ( Control system and device for patient assist, 2013). Another example, a chair-like device that assists users to rise after a fall by lifting them up. However, in these solutions, there is a need for a third-party assistance to deliver the chair and assist the user ( Google Patents, 2022). Furthermore, a sling-like device is needed to lift the user after a fall, and then transport him/her with lifting and mobility mechanisms to the chair or bed. The device can be used for different purposes; however, it is mostly used in hospitals for lifting patients when needed ( Hakamiun, 1999).
In addition to devices that assist users after a fall, there are also devices that detect falls either during or after happening, which account for the majority of devices in the market ( Abdul Rahman et al., 2021). Wearable fall detection devices use an accelerometer to detect falls when they happen. During a fall, the accelerometer triggers the system to send an alert to a previously designated personnel. The detector is located mostly on the waist (lumbar area) ( Huang and Chan, 2014; Bet et al., 2019). Another technique is mounting detection cameras on walls, which detect a fall when any part of the body touches the ground (except the feet, to prevent false-positive detection when a person is walking) ( Wang et al., 2020; Bayen et al., 2021).
To this end, this study aims to design a device that assists users to rise after a fall independently while maintaining the device’s mobility, low cost, and easiness of use (no third-party assistance needed). The proposed device should be able to withstand vast range of weights and heights. Furthermore, this study aims to analyze total deformation and von-Misses stresses on the design by using finite element analysis (FEA) methods to ensure the suitability of design to withstand applied loads.
METHODS
Operational steps
The focus in this study is to design a device that can carry a heavy weight senior or patient and be mobile at the same time. The walker’s design was based on a conventional standard walker size with a base width and depth of 52 and 50 cm, respectively. The height of a walker is adjustable and usually is in the range of 77 to 95 cm. However, the height of the proposed design will vary as will be mentioned afterwards. The general idea of the proposed design is a walker aid with piston leg support and a foldable seat; the seat can be rotated by 90 degrees to allow the senior to sit on. The piston allows the walker to be lowered to half of the leg length and assists the senior during the rising action ( Fig. 1). A three-dimensional computer aided design (3D CAD) model was designed by using SolidWorks 2017 (Dassault Systems, Waltham, MA, USA). As shown in Figure 1, (A) is the walker’s grip on which the user will support him/herself and move the walker as needed. The walker’s grip needs to be comfortable (soft on the hands) as well as strong to handle the force created by the user’s weight. (B) is the seat that is connected to the pole (C) which is also attached to the grip (A). (D) and (E) are the pistons that are responsible for the ascendance and descendance of the walker aid.
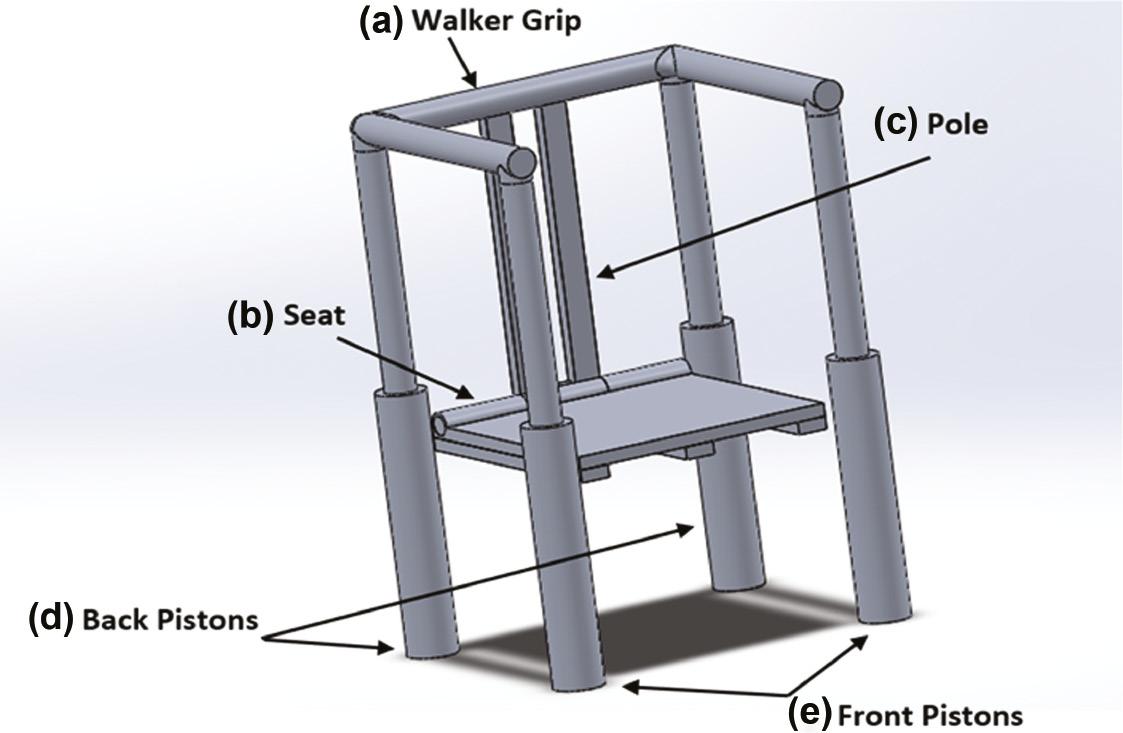
Fully assembled device parts. (a) The walker hand grip. (b) The seat which is supported by pole (c). (d and e) Back and front pistons which perform the lifting mechanism.
As shown in the steps of the operation flow chart below ( Fig. 2), when a user falls, he/she should press a button which will cause the seat to rotate by 90° from the standing position to the seating position ( Fig. 2a and b). This will cause the piston to lower itself by half the height by which the seat will reach the ground ( Fig. 2b and c). Then, the senior can sit on the seat that is flat on the ground and press the button again which will result in the pistons going back to their original height. After that the seat will be in the normal standard seating high (around 45 cm from the ground) ( Fig. 2b) allowing the senior to stand up again as if they are standing up from a normal chair. After the rise of the senior the seat will lock to its initial standing state ( Fig. 2a) allowing the senior to use the walker as a conventional walker again.
Stress analysis
Stress analysis using the von Mises yield criteria is used to study the material’s yield point and show the locations of stress concentration on the actual design. Von Mises analysis is mostly used for ductile materials such as metals, of which aluminum was used for this walker. Furthermore, total deformation was investigated, which measures how much plastic strain the model is facing due to external loads. For the FEA simulation, aluminum alloy was assumed for the U-shaped walker grip due to its lightweight and durability, which is expected to be used in the prototype to make the walker light and mobile. For the pistons and seat supporting pole, stainless steel was used due to its high stiffness and endurance.
RESULTS
Finite element analysis
For FEA, Ansys 2022 R1 (Ansys Inc., Canonsburg, PA, USA) was used to perform static structural analysis on the proposed design to get total deformation and von Mises stresses on the walker’s different parts.
The walker system was meshed as shown in Figure 3a using tetrahedral elements, as this element type is suitable for irregular meshes. The number of nodes in the model was 88,400 and the number of elements was 47,187 with a size of 2 cm = 0.02 m. The walker was fixed (boundary conditions) at the base of each piston at the bottom of the four pistons. This was done at full expansion and full retraction of the four pistons ( Fig. 3b and c).
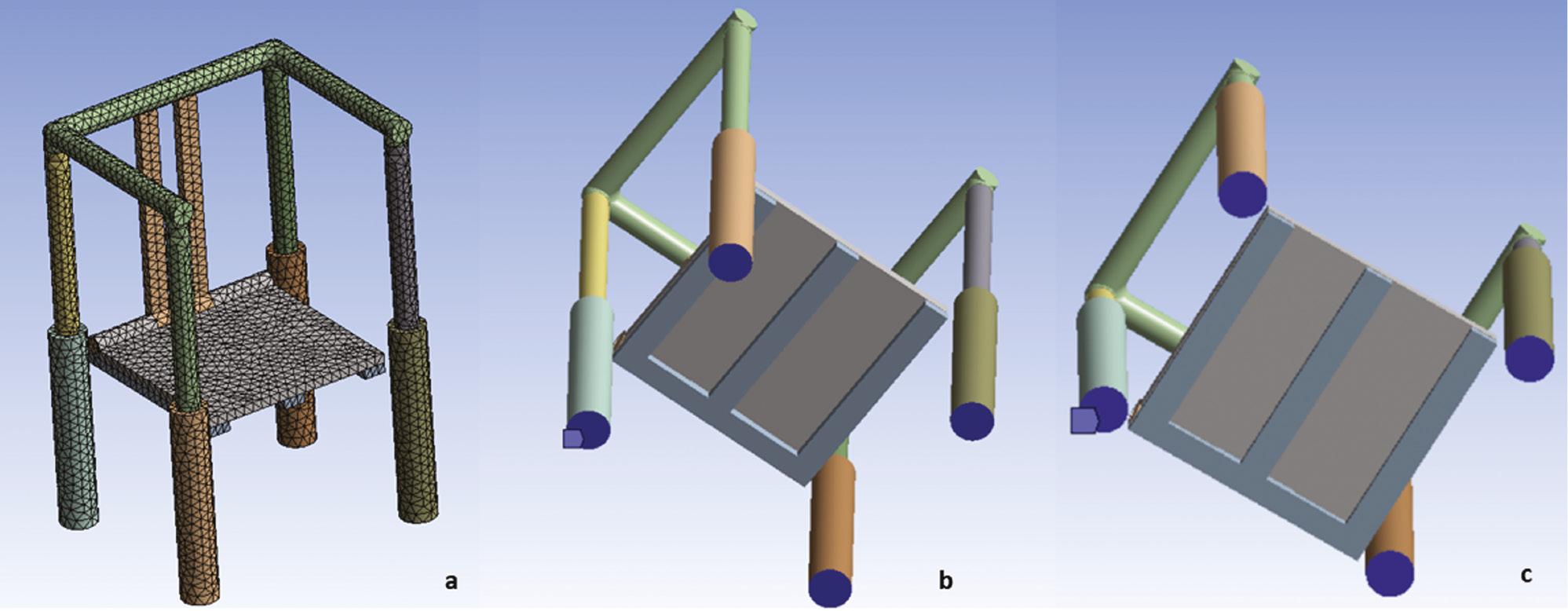
Finite element meshed walker (a), walker fix points (boundary conditions) at full expansion of pistons (b), and full retraction of pistons (c).
The walker was fixed at the base of the pistons and two loads were applied separately. The first load was applied on the seat with a magnitude of 1400 N (i.e. a mass of approximately 142 kg) while the seat was elevated and lowered, respectively, as shown in Figure 4. The second load was applied on the grip with a magnitude of 504 N on each side, which is considered 36% of the senior’s weight during a full stand up ( Fig. 4c) ( Youdas et al., 2005).
Weight impact on the seat
When the seat was lowered to the smallest distance above the ground, by fully retracting all pistons, and a load of 1400 N was applied to the seat as shown in Figure 5, the total deformation was increasing starting from the supporting pole (96.07 μm) to the distal end of the seat (245.41 μm - maximum deformation) ( Fig. 5a). However, the supportive pole and the grip experienced lower deformation, 66.04 and 5.52 μm, respectively. The von Mises stress analysis shown in Figure 5b shows that a maximum stress of 19.78 MPa was in the connections between parts (i.e. seat and poles).
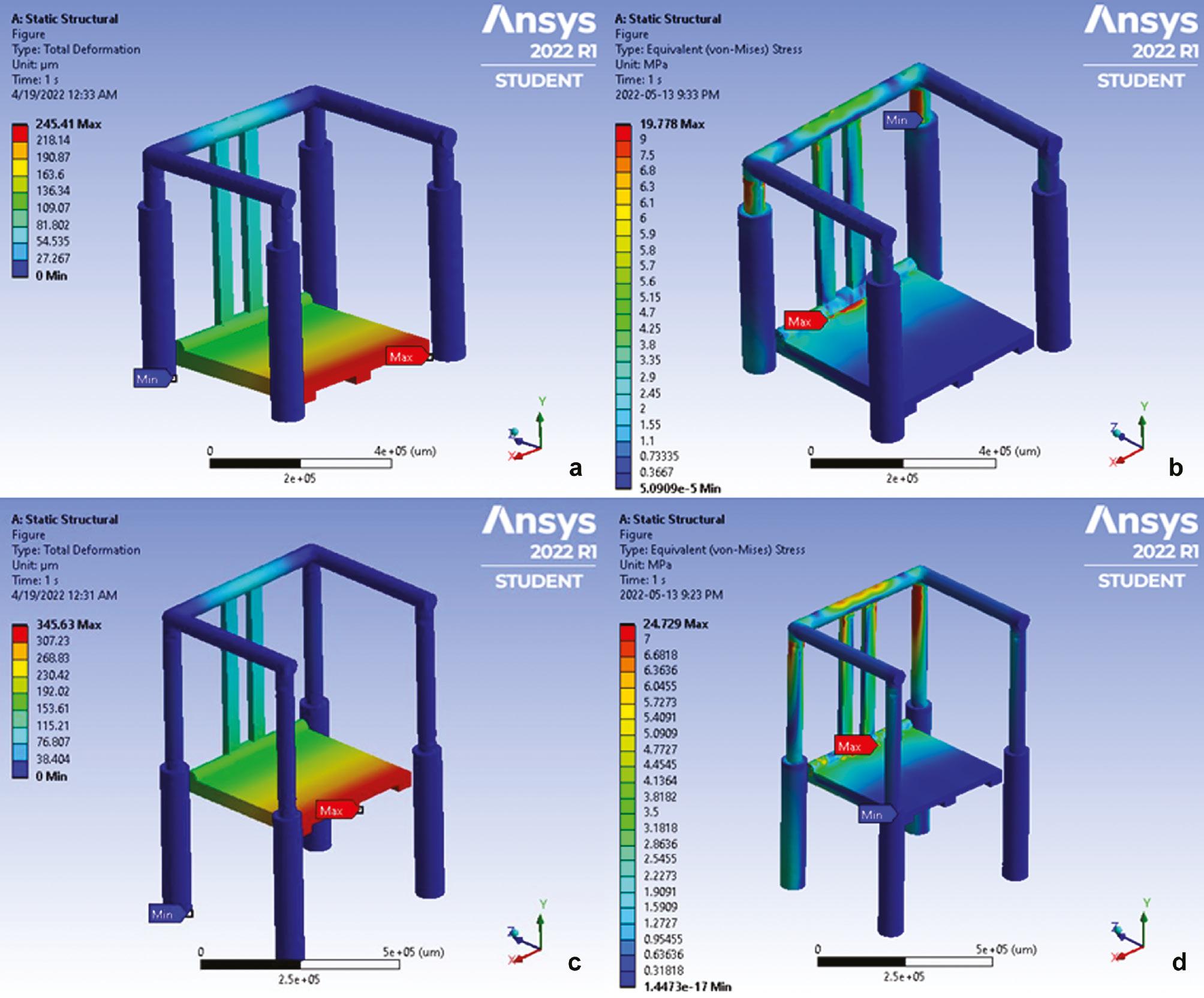
Full retraction and expansion of piston results. (a) Total deformation and (b) von Mises stress at retracted pistons. (c) Total deformation and (d) von Mises stresses at full expansion of pistons.
When the pistons are at full expansion, the total deformation was increasing from the supporting pole (153.61 μm) to the distal end of the seat (345.63 μm - maximum deformation). Regarding the von Mises stresses (d), the maximum stress was 24.73 MPa at the connection between the seat and the supporting pole.
Weight impact on the hand grip
Figure 6a shows that the maximum deformation was located where the user holds the walker aid with a magnitude of 16.43 μm. Concerning von Mises stresses ( Fig. 6b), the maximum stress is located at the connection between the piston and hand grip with a stress of 3.57 MPa.
DISCUSSION
The present research was aimed to design a mobile and easy to use after-fall-assistive device based on a conventional walker. For the CAD model, Solidworks 2017 was used, and FEA was performed by using Ansys 2022 R1 to analyze von Mises stresses and the total deformation on walker aid as a whole and during operation. It was found that the von Mises stresses reached a maximum of 24.73 MPa. And it was found that the total deformation reached a maximum of 345.63 μm.
The results of the weight impact on the seat indicate that the total deformation of lowered pistons ( Fig. 5a) on the pole was 96.07 μm and the amount increases until it reaches the distal end of the seat which has a maximum deformation of 245.41 μm on the seat. This is due to the seat support location and connection in which the supporting pole is located at one end of the seat only, while the distal end (i.e. other end) of the seat has no supports to allow the user to access the seat. Regarding the fully expanded pistons ( Fig. 5c), the maximum total deformation was 345.63 μm which was greater than that of fully retracted pistons due to the lack of support of the ground under the seat and the higher the center of gravity of the patient. The deformation of the seat from the furthest end can be managed by adding a rope or a metal string that passes under the seat and latches to the grip. This string will act like a hanged bridge’s main/suspender cables.
As for the von Mises stress analyses for retracted ( Fig. 5b) and expanded ( Fig. 5d) pistons, the maximum stress values on the hinge were 19.78 and 24.73 MPa, respectively, which does not exceed the yield strength of the chosen material (i.e. yield stress for SAE 304 stainless steel is 515 MPa and that for 6061 aluminum is 110 MPa), taking into consideration that it is subjected to a load of 1400 N (i.e. a mass of 142 kg). Additionally, the results of the FEA show that when the pistons are at full height the maximum stress is larger in comparison to when the pistons are lowered. This is due to the support of the lead screw inside the piston tube. The von Mises stress on the hand grip ( Fig. 6b) as a result of the user’s weight shows that the maximum stress was 3.57 MPa in the connection between the piston and hand grip due to the higher load of the upper body in comparison to the lower body. Von Mises stress analysis shows that the device experienced significantly lower stresses than the yield stress of the material. Given that, the safety factor of the material is approximately 515/24.73 = 20.82 for stainless steel and 110/3.57 = 30.81 for aluminum.
The design of the device combines two ways of assistance. In the expanded position the device prevents the user from falling with four point of floor contact to increase the area of support base and keep center of gravity within the device, which allows more stable walking action. In the incident of falling, the user can push a button once to open the seat and lower the pistons to half the height of the device conveniently. Then, the seat will be located at the smallest distance above the ground which allows the user to sit on. After that the user has to press the button again to raise him/her up with the pistons. The mobility of the design allows the user to have the device most of the time with him/her to use as a conventional walker or as an after-fall-assistive device.
As mentioned earlier in the introduction, there is a general issue of rising up after a fall especially for seniors and people with diseases that affect their balance such as multiple sclerosis, arthritis, Parkinson’s disease, osteoporosis, etc., as more than half of them stay on the floor for more than an hour. After a fall, 75% of seniors visit the doctor’s office and 33.3% call for healthcare professionals ( Choi et al., 2019). During hospital discharge, they advise patients to get home care services (i.e. home health agencies and visiting nurse) for the concern from the risk of falling, in addition to providing assistance if a falling incident occurs ( Ang et al., 2020). The CDC shows that falling once among seniors and obese individuals doubles the chances of falling again ( CDC, 2022a). Due to the high cost of home care, low salary is considered as a risk factor, and 54% of middle-income individuals cannot afford health care and functional needs ( Pearson et al., 2022). Obese individuals who have a BMI ≥40 kg/m 2 have a 16% higher risk of falling than nonobese individuals ( Neri et al., 2020; Alabdullgader and Rabbani, 2021). Therefore, obesity has also been associated with an increased risk of multiple falls. Obese individuals are less likely to sustain hip fractures. However, humerus, leg, and ankle fractures are more likely to occur ( Neri et al., 2020). The results indicate that the model is able to withstand a load of 1400 N, which corresponds to a senior with a mass of approximately 142 kg who is considered obese.
There are some restrictions in this study; first, the mesh element size of the model was limited to a relatively low-resolution mesh due to licensing issues of Ansys 2022 R1 (Ansys Inc., Canonsburg, PA, USA) software. Second, a physical prototype of the model was not built. This will be considered in future work.
CONCLUSION
This study focused on designing a device to support individuals after fall withstanding a fairly large weight. A 3D CAD design was modeled according to the standard dimensions of a conventional walker aid. FEA was performed which showed that the design can lift an overweight individual with a weight of 142 kg and still being able to withstand heavier weight. The results of FEA could be the reference in any future improvement of the design.