INTRODUCTION
A prosthetic leg or limb is an artificial limb that is used to replace a biological limb in humans. A prosthesis is necessary when a person loses a limb as a result of an accident, congenital disability, war, etc. Between 110 million and 190 million people living in developing nations were estimated to have impairments in 2015, with more than 90 million of those people being children (Sundararaj and Subramaniyan, 2020). By 2025, it is expected that more than 25 million people worldwide would need orthotic or prosthetic devices (Abood and Faidh-Allah, 2019; Solis et al., 2021; Talla et al., 2021). The demand would still be great now. Many people do not have access to these prosthetic devices, especially for sports usage, due to poverty, high prosthetic costs, and a shortage of technicians. Metals and other alloys are currently being used to make prostheses for modern sports that imitate the functions of a real human limb (Hagberg et al., 2005; Jayaraman et al., 2019; Krausz and Hargrove, 2019; Parga and Yu, 2019; Villarreal and Gregg, 2019; Damerla et al., 2022; Gomez-Correa and Cruz-Ortiz, 2022). Artificial limbs are more expensive than mechanical prostheses, which is a disadvantage for lower-middle-class economies because they will not be able to afford such high prices (Mauroy et al., 2012; Devaraj et al., 2020; Migliore et al., 2020; Powell et al., 2020). Nevertheless, they provide necessary features and help close the gap between mechanical and automated prostheses. There is a fusion between sports and prosthetics, which has resulted in a new era of sophisticated prostheses that have enhanced the game and helped to reach new heights. Athletes have been using artificial body parts for sports prosthetics for several decades now, and this has led to the development of high-quality competition prosthetics for athletes (Funken et al., 2014; Lathers and la Belle, 2016; Bae et al., 2017; Muta et al., 2020; Brack and Amalu, 2021; Revilla-León et al., 2021). There has been research demonstrating that prosthetics technology can be beneficial to future performance as well as to an individual’s emotional conditions. Furthermore, certain activities such as swimming can provide therapeutic benefits for individuals with amputated lower limbs (Noroozi et al., 2013). For swimmers with limb losses who are interested in both fitness and competition, the Paralympic Games offers a competitive environment. Considering the prospects for sports participation for persons with limb impairments, physicians and prosthetists are trying to develop innovative prosthetic designs of their own. Physicians and prosthetists should consider the athlete’s wants and preferences, as well as the functional demands of the selected sports activity when writing a prosthetic prescription (Helm et al., 1986; Hagberg et al., 2008; Webber and Davis, 2015; Mundell et al., 2016; Farrokhi et al., 2018; Castellini, 2019; Johannes et al., 2019; Yu et al., 2021). Nevertheless, cutting-edge technology and the use of innovative materials have developed this business beyond simply providing players with the ability to partake in their favorite activities.
Although there are many diverse uses for prosthetic limbs, the usage on which this study focuses falls under the category of prosthetic upgrades (Jönsson et al., 2011). Special prosthetics known as prosthetic improvements enable patients to engage in more strenuous leisure activities like jogging. Figure 1 shows an example of a prosthetic running blade used by athletes. Due to the intense demands of athletic competition and the desire of people with lower-limb amputations to participate in sports, energy-storing and energy-returning feet have been developed (Gallagher and MacLachlan, 2004). These feet may store energy during stance and restore it to the wearer in late stance to aid in forward propulsion. The running blades are made from different materials as mentioned elsewhere (Grimmer et al., 2014; Petrone et al., 2020; DeVillez et al., 2022; Siddiqui et al., 2023).
The blade aims to mimic running as accurately as possible; as a result, it lacks a copy heel as natural running does not utilize one. Similar to regular running shoes, blades can be equipped with running spikes to help them better grip the track (Grimmer et al., 2014; Liu et al., 2017; Chereshnev and Kertész-Farkas, 2018; Frossard et al., 2019; Petrone et al., 2020; Rankin et al., 2020; Emonds and Mombaur, 2021; Aftab and Ahmed, 2022; Murabayashi et al., 2022; Shim et al., 2022). In the next section, we have summarized the latest research outputs in this area. In this work, we carried out a three-dimensional finite element analysis (FEA) of a prosthetic running blade under various static loads to simulate and analyze the structural behavior of the blade. Furthermore, we have outlined our research objectives and methodology in the next section.
BACKGROUND
Recently, several researchers have carried out work on the design and development of high-performance running blades. In this section, we have summarized some recent and important research studies on the design and development of running blades. Rahman et al. (2014) numerically studied prosthetic blades using FEA. They studied how to enhance the performance of running blades, especially the design of commercially available Ossur products. Two specific materials for investigation were selected, namely, polyethylene epoxy and vinyl ester. It was demonstrated that new materials can reduce the strain in a running blade body and also it needs less amount of carbon fiber layers. This new design also helped them to reduce the weight of the overall body. It was also mentioned that three different designs were studied Cheetah blade, Flex-Run blade, and Flex-Sprint blade. Natural fiber and composite laminated materials are now becoming main-stream materials to design running blades. Shastry et al. (2021) studied the dynamics of prosthetic legs. They mentioned that disabled people can easily and actively use prosthetic legs because the new designs significantly provide sufficient torque and force. One of the major concerns about prosthetic legs is their cost and it is expected that new materials can be affordable to lower-income people. Also, cheaper prosthetics that are not designed precisely due to a lack of advanced materials could affect the walkability of disabled persons. It is also important to understand the different behavior and dynamics of prosthetic running blades. In the quest to understand the deformations such as buckling, bending, and relaxation, Ouarhim et al. (2021) investigated laminated composite materials. They investigated woven and chopped strands mats of polyester and glass fiber. The research investigation was based on experiments and finite element simulation. They made a comprehensive study on materials design and tests. They concluded that the relaxation dynamics of running blades depend upon the design and choice of material. Most of the researchers have focused on either the materials or the design of prosthetic running blades. Mechi and Al-Waily (2021) studied the stress and deformation in the running blade. It is well evident that prosthetics are prone to stress and deformation and careful design could give the best performance to disabled persons. In this work, they chose natural kenaf fiber along with other reinforcement fibers. The investigation was carried out on experimental along with numerical modeling. The results showed that von Mises stress was equal to 34.14 Mpa for the experimental F-Socket test. Furthermore, the results were compared with the numerical modeling results and it was within the acceptable range. The design aspect of prosthetic legs and limbs has been widely discussed by Safari (2020) in their review research work. They mentioned that new technology of materials is assisting in developing advanced kinds of running blades. Migliore et al. (2020) studied the biomechanical effect on prosthetic sockets of gold medal Paralympic sprinters. They studied different cases of socket design on a female sportsperson. They measured reaction forces in terms of kinematics and moments. In the end, they concluded a certain design of sockets was most comfortable for the sportsperson.
Some authors have researched to enhance the mechanical properties of the socket which is used for below-knee prosthetics (Kadhim et al., 2018). The composite materials (Kevlar) were used to make sockets, and stress and deformation were studied. The composite materials were used in layer form and seven layers were utilized in their experiments. The results obtained through experiments depicted that the new design has 96% similarity with the intact leg (Jweeg et al., 2019). An amputee must be fitted with a well-designed lower-limb prosthesis to regain normal locomotion. In another aspect of easing the use of a prosthetic limb, Kadhim et al. (2018) explored the novel mechanism for the knee joint. The new design was able to give flexibility of 90-degree rotation to the disabled person. They especially mentioned the aluminum alloy 6061, 7075, and AISI 4130 Steel material for knee joints.
Furthermore, the design process of prosthetics depends highly upon making prototypes and its experimental and simulation testing. The enhancement in performance is achieved by iterative ways of designing and trials. The important aspect of the design is to provide realistic motion of absent limbs with ease. Thus, at different applications and paces, experts have different physiological impacts on the human body. Tryggvason et al. (2017) worked on the idea of finding stiffness characteristics of ankles using the finite element method. The results were validated with the actual device. It was important to note that the model was enhanced to substitute added flexibility and damping during ankle motion. In addition to this, Colombo et al. (2016) studied the limb socket to improve its design and performance. They studied pressure distribution using finite element simulation. The results highlighted the improved model of the limb socket. To know the effect of advanced materials on prosthetic legs, Rahman et al. (2014) used different kinds of composite materials. In their research work, it was mentioned that polyethylene epoxy and Vinylester thermoplastics along with carbon fiber can reduce the weight and cost of each part. They also mentioned that better prosthetic performance can be achieved by using carbon fibers. The research work was focused on different designs, namely, the Cheetah blade, Flex-Run blade, and Flex-Sprint blade. A good prosthetic design has several important characteristics such as realistic flex near human leg muscle, less energy loss, and comfort. Noroozi et al. (2013) studied the natural frequencies, damping, and mode shapes of prosthetic running blades. They mentioned that a better design of the running blade should be energy-storing and returning the energy for forward motion. They worked on modal analysis of commercially available running blades. The results suggested that dynamic analysis is important for understanding and designing a high-performance running blade. As we have noted from most of the research literature, emerging materials can enhance performance and reduce the cost of running blades. This will help poor and marginalized disabled persons to participate in sports thus creating a society that has moral and emotional support for disabled persons. It is worth noting that advanced materials and design processes would radically change the way prosthetics are currently made (Powell et al., 2020).
The existing literature reveals a limited amount of research conducted on the influence of materials on the static behavior of prosthetic running blades when subjected to loads associated with standing, walking, and running. Our objective is to analyze the static behavior of prosthetic legs made of aluminum alloy (2024 T4), stainless steel alloy, titanium alloy, and carbon fiber. In this work, we have carried out a three-dimensional FEA of prosthetic running blade under various static loads. Furthermore, we also studied the comparison of different materials on structural performance. In addition to this, we have also made a cost analysis to know the best and cheapest running blade in terms of material cost.
MATERIALS AND METHODS
In general prosthetic running blades are made to mimic exactly like natural human parts and perform realistically. Furthermore, it should be light in weight for optimal comfort and also durable. Nowadays, most of the running blades are made from metal aluminum alloy (2024 T4) and composite materials. Especially, some new advanced materials such as polymers, fiber metal laminates, and composites have shown high-performance properties. In this work, we have used four popular materials for running blades, namely, aluminum alloy (2024 T4), stainless steel, carbon fiber, and titanium alloy. We have used a similar design of a commercially available running blade by Levitate Technology ApS (Roskilde), Denmark. The design of the running blade has been studied very carefully and transformed into a three-dimensional Computer Aided Design (CAD) model. The geometry has been made on SpaceClaim software (Ansys Inc., Canonsburg, PA, USA). Furthermore, meshing and structural analysis has been carried out on Ansys Mechanical software. In this numerical work, the force has been applied on the top of the assembly of the running blade. We have considered three different postures for sportspersons such as standing, walking, and running. Table 1 illustrates the force related to every three postures. The force was applied vertically to the running blades for static behavior analysis.
In this study, we have carried out a numerical analysis of four different materials. We studied the mechanical behavior of running blades during different conditions of users such as standing, walking, and running. The mechanical properties of materials are given in Table 2. We used the Ansys Finite Element module to simulate the running blade behavior under different test loads. The design of the running blade is inspired by the commercially available running blade. The dimensions and meshing details of the running blade are presented in Figure 2a. There are four components of the running blade as shown in Figure 2b along with dimensions. The element mesh has been shown in Figure 2c and d. In this numerical model, we have chosen a specific number of elements by grid independency test. The details of mesh size and the number of elements are illustrated in Table 3. We took total deformation at the midplane of the running blade as the criterion to judge the suitability of the number of elements. From the results of total deformation, we concluded that a mesh size of 66,071 is the most suitable for producing acceptable results. Furthermore, we validated our finite element model with previous work by Ouarhim et al. (2021). Figure 3 shows the comparison of total deformation from our current model and the work of Ouarhim et al. (2021) We found that our results are under the limit of 2.5% of variations.
Material properties (Noroozi et al., 2013; Sundararaj and Subramaniyan, 2020; Ouarhim et al., 2021; Talla et al., 2021).
No | Property | Materials | |||
---|---|---|---|---|---|
Aluminum (2024 T4) | Steel (AISI 316 stainless steel) | Carbon fiber | Titanium alloy (titanium Ti-6Al-4V (grade 5), annealed) | ||
1 | Modulus of elasticity (GPa) | 73 | 193 | 230 | 96 |
2 | Poisson’s ratio | 0.33 | 0.31 | 0.2 | 0.36 |
3 | Yield strength (MPa) | 324 | 207 | 2500 | 930 |
4 | Tensile strength Ultimate (MPa) | 469 | 586 | 3590 | 1070 |
5 | Comp. strength (MPa) | – | 207 | – | 930 |
6 | Density (kg/m3) | 2780 | 7750 | 1750 | 4620 |
7 | Melting point (C) | 638 | 1400 | 3652 | 1660 |
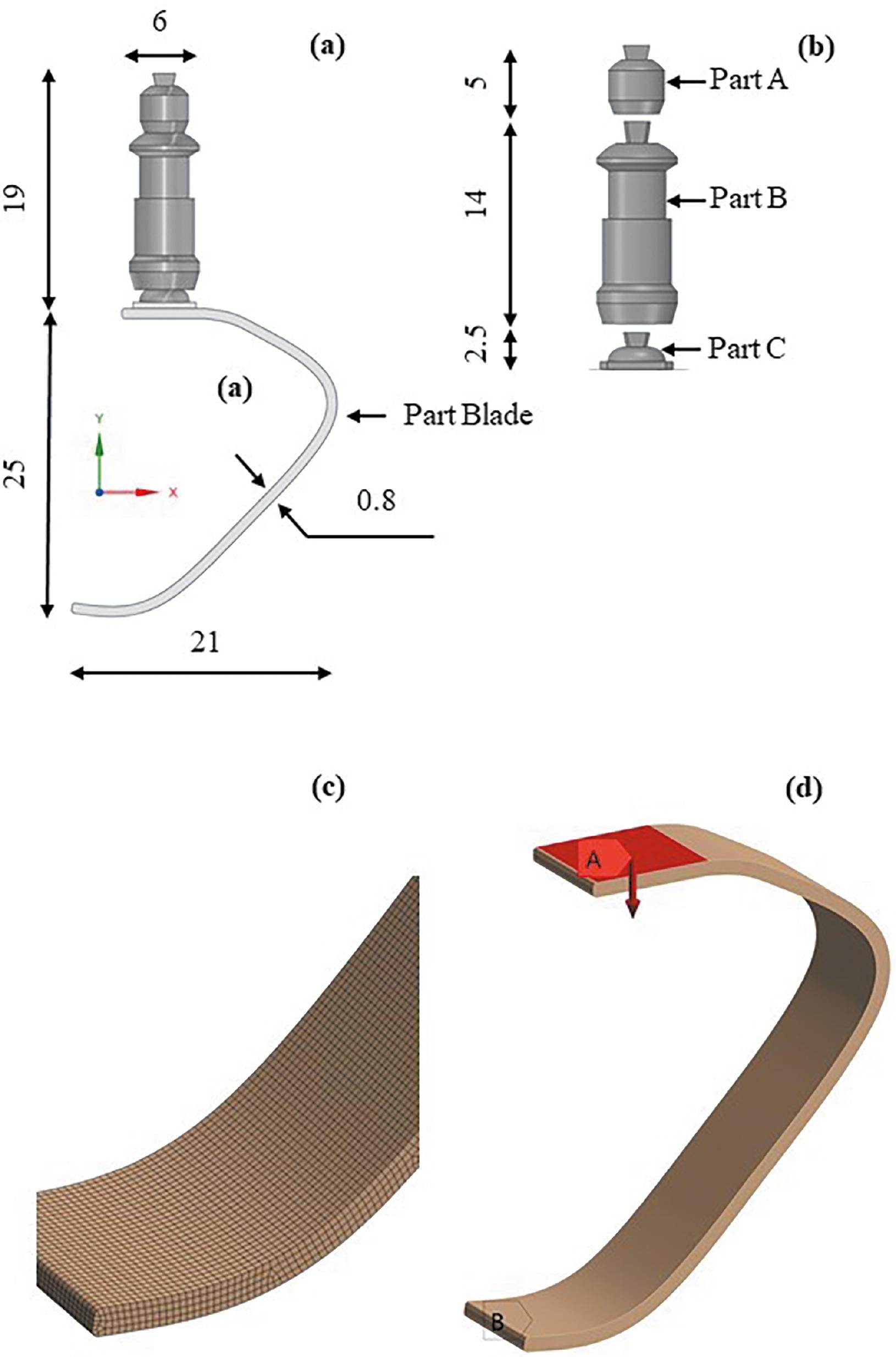
Details of the prosthetic running blade. (a) Dimensions of the running blade. (b) Top parts of the running blade. (c) Meshing. (d) Point load (all dimensions in mm).
RESULTS AND DISCUSSION
Total deformation
Figure 3 shows the total deformation in the prosthetic running blade. We have observed total deformation on four different materials. The design of the running blade is quite similar to that of the commercially available running blades. In this figure, we compared the mechanical behavior of aluminum 2024 T4, AISI 316 stainless steel, carbon fiber, and titanium Ti-6Al-4V (grade 5). We did a simulation of deformation based on three load conditions such as 700 N for normal walking conditions and 1400 N and 2100 N for running conditions. Figure 3 shows the deformation under 2100 N load on the running blade. It is observed here that the maximum total deformation is 29.48 mm for aluminum alloy (2024 T4), shown in Figure 3a. The maximum total deformation for AISI 316 stainless steel is 19.88 mm (Figure 3b). Furthermore, it is observed that carbon fiber goes to 17.57 mm deformation as shown in Figure 3c. The added advantage of carbon fiber is that it is lightweight and stores energy as well. Figure 3d shows the deformation value of 26.14 mm for titanium Ti-6Al-4V (grade 5).
Figure 4 shows the total deformation of the prosthetic running blade. The plot has been made concerning four different materials under variable load conditions. It can be observed here that aluminum alloy (2024 T4) has a higher deformation rate as compared to the other three materials. The aluminum alloy (2024 T4) is a tempered alloy by heat treatment and a natural aging process. Thus, it has good ductility. Besides, it has a high strength-to-weight ratio making it one of the suitable materials for manufacturing prosthetic legs. However, it has average machinability but poor corrosion resistance. So, this could be a negative aspect of choosing this material for a prosthetic running blade. Furthermore, cladding and protection film would help it to make corrosion resistance. The titanium alloy had shown a similar kind of behavior. However, total deformation based on variable load conditions is slightly less than that of the aluminum alloy (2024 T4). The titanium alloy (Ti-6Al-4V, grade 5) is the most popular alloy of titanium, which has a lightweight and high strength ratio. This makes this alloy an excellent material for a prosthetic leg. But the cost associated with titanium alloy is very high. Hence, a final product may have a higher cost tag. In addition to this, we also investigated that the total deformation in prosthetic legs made of carbon fiber has the least total deformation during variable load conditions. Figure 3 also illustrates the mechanical behavior of steel. It can be noted here that the carbon fiber-based prosthetic running blade has performed superior to the standard steel blade.
Total deformation in the x-direction
Figure 5 shows the total deformation in the x-direction under 2100 N static load. The contour also illustrates the effect of deformation using different types of materials. The x-directional deformation is important in the aspect of loading and bending. Thus, a critical study needs to highlight the directional deformation. It can be observed in Figure 5a that the maximum deformation is 2.35 mm in the x-direction. It is worth noting that a significant deformation of joints happened in the negative x-direction. In addition to this, it can be observed that the lower and mid part of the prosthetic running blade has deformation in the x-direction. This could impact the storage and release of energy. A similar deformation can be noted in Figure 5b-d. The directional deformation value is least in the carbon fiber material as compared to the other three materials. The deformation in the x-direction concerning different forces is shown in Figure 6. It is apparent that aluminum 2024 T4, which is ductile in nature, has higher deformation in the x-direction. Furthermore, carbon fiber has shown excellent mechanical behavior in terms of handling shear stress (lowest deformation).
Equivalent (von Mises) stress
The yielding of the prosthetic running blade can be predicted by an equivalent von Mises Stress plot. In actual conditions of running, loads on running blades are from different directions. Thus, taking the magnitude of all stresses of the running blade would reflect equivalent stress. These equivalent stress values are useful to estimate the material’s strength and durability. Furthermore, von Mises’s stress has a meaningful impact on material selection. Figure 7 shows the equivalent (von Mises) stress for different materials for the running blade. It can be noted here that equivalent stress is higher for aluminum alloy (2024 T4) as compared to other materials. Furthermore, carbon fiber has the least value. The yield limit of carbon fiber is around 2500 MPa, which makes it an excellent choice for the running blade. If the equivalent stress (von Mises) of the running blade increases beyond the yield limit of materials, then the component of the running blade will start yielding. The equivalent stress for the running blade (under 2100 N static load) is shown in Figure 8. A closer look at the middle part of Figure 8a can show the maximum equivalent stress patch, which is around 570 MPa. In Figure 8b, the equivalent stress value lies around 514 MPa and spreads over a larger portion of the running blade. Furthermore, the carbon fiber-based running blade has remarkable performance, as can be seen in Figure 8c. Moreover, Figure 8d shows the equivalent stress contour spread over a titanium alloy running blade. The values of equivalent stress are still under the yield value of the material.
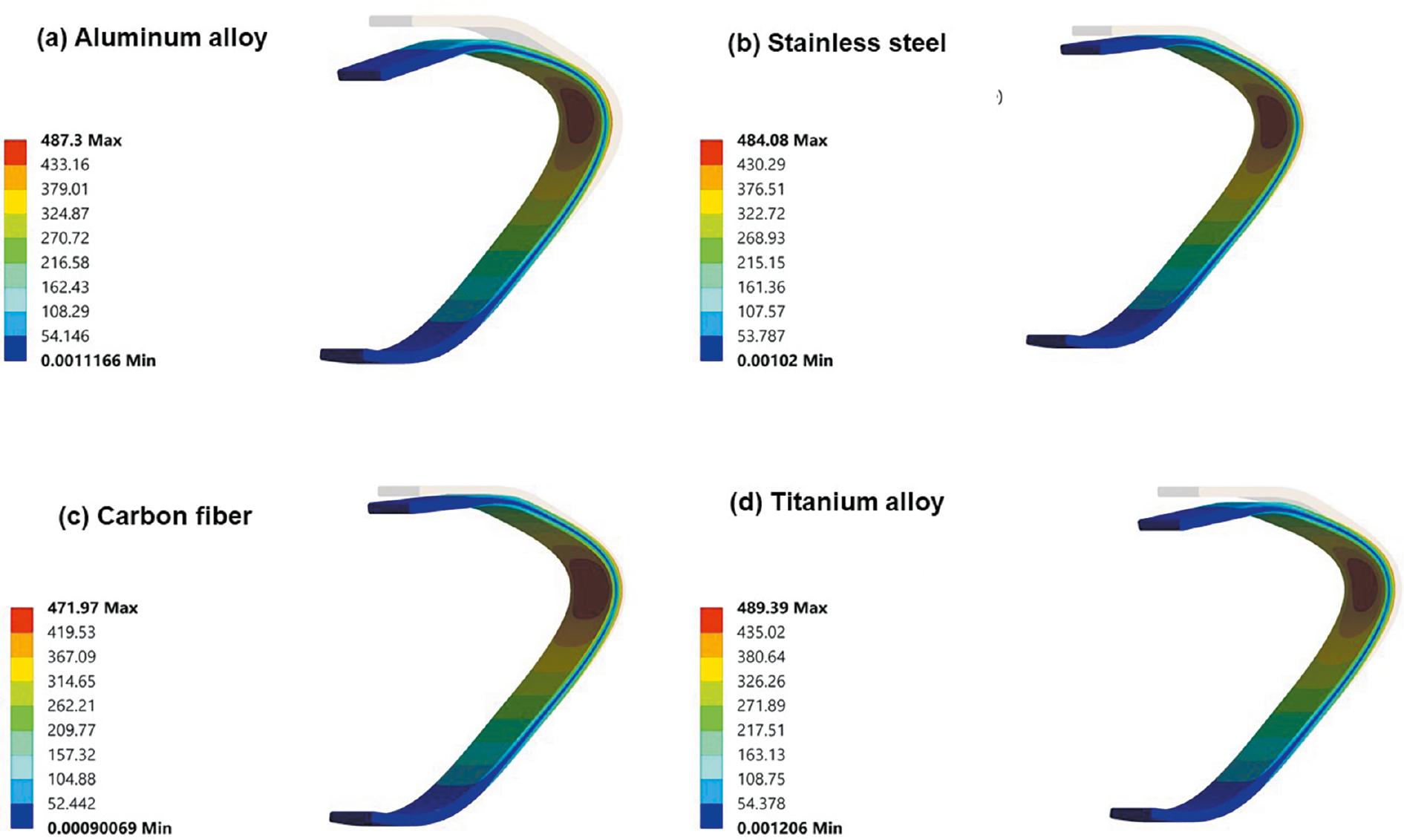
Equivalent (von Mises) stress contour at 2100 N force: (a) aluminum alloy, (b) stainless steel, (c) carbon fiber and (d) titanium alloy (Unit: MPa).
Figure 9 compares the equivalent stress (von Mises), maximum principal stress, and shear stress for four selected materials. This plot is beneficial to analyze and understand the corresponding values of each stress and their relationship. Since research work on the prosthetic running blade is in the infancy stage in terms of numerical modeling, the fundamentals of these values must be presented in a lucrative manner. It can be noted here that maximum principal stress is higher as compared to others too because the static load has been utilized in this numerical work. Further equivalent stress values are important to know the distortion energy density in a running blade under load. It can be also noted here that shear stress values are smaller for stainless steel. The predicted value of total deformation versus strain energy is shown in Figure 10. In addition to these, all four materials have been presented to set the understanding of performance. The strain energy correspondence to the elastic potential energy received by the prosthetic running blade during deformation. It can be observed from Figure 10 that strain energy is proportional to the total deformation in aluminum alloy (2024 T4) and titanium alloy. However, strain energy (the stored energy in prosthetic running blades) is significantly less in carbon fiber and stainless steel. The reduction in strain energy is a great advantage to improve the performance of the running blade.
COST ANALYSIS
In addition to the performance study, cost analysis is one of the important aspects of manufacturing prosthetic running blades. Therefore, we have studied the cost of materials for prosthetic running blades. However, we have not considered the manufacturing cost. Table 4 presents the dimensions and weight distribution of four parts of the running blade. In this case, we have assumed that parts A, B, and C will be made from aluminum 2024 T4 alloy because of its availability and price. Furthermore, part blade (D) will be manufactured from different materials as shown in Table 4. We have gathered cost information from various sources as it is available in Saudi Arabia. Table 5 shows the cumulative cost of the running blade for each different material. It can be noted that carbon fiber seems to be the most lucrative choice due to having a minimum price per kilogram. The total material costs for aluminum alloy (2024 T4), stainless steel (AISI 316), carbon fiber, and titanium alloy (grade 5) are 20.9, 67.6, 48.5, and 78.1 USD, respectively. The material cost of titanium alloy is higher when compared to that of others.
Dimensions and weight distribution of prosthetic leg.
Running blade materials | Parts | Dimension (mm) | Volume (mm3) | Weight (kg) | Price (USD/kg)a | Material cost (USD) |
---|---|---|---|---|---|---|
Aluminum 2024 T4 | Top parts (A) | 50 × 50 × 40 | 36,450 | 0.10 | 10 | 1 |
Aluminum 2024 T4 | Middle parts (B) | 56 × 56 × 140 | 216,130 | 0.60 | 10 | 6 |
Aluminum 2024 T4 | Bottom parts (C) | 50 × 50 × 25 | 27,150 | 0.75 | 10 | 7.5 |
Aluminum 2024 T4 | Blade (D) | 460 × 60 × 8 | 228,700 | 0.64 | 10 | 6.4 |
AISI 316 stainless steel | Blade (D) | 460 × 60 × 8 | 228,700 | 1.77 | 30 | 53.1 |
Carbon fiber | Blade (D) | 460 × 60 × 8 | 228,700 | 0.40 | 85 | 34 |
Titanium alloy grade 5 | Blade (D) | 460 × 60 × 8 | 228,700 | 1.06 | 60 | 63.6 |
aBased on the price available at local merchant in Saudi Arabia.
Cost analysis of materials used to manufacture the running blade.
Running blade set | Parts details | Blade materials | Total material cost (USD) |
---|---|---|---|
1 | Part A + B + C + blade | Aluminum 2024 T4 | 20.9 |
2 | Part A + B + C + blade | AISI 316 stainless steel | 67.6 |
3 | Part A + B + C + blade | Carbon fiber | 48.5 |
4 | Part A + B + C + blade | Titanium alloy grade 5 | 78.1 |
CONCLUSIONS
Prosthetic running blades are an important device that enables affected people to participate in sports, thus, helping them to improve their physiological and psychological conditions. Following are the conclusions drawn from our research work:
A prosthetic running blade could solve the problems for the disabled person participating in sports activities, consequently, it will improve the physical and mental balance. Furthermore, the availability and price of prosthetic running blades limit the choices for disabled persons.
Considering these situations, we have studied the performance of running blades made of four different materials, namely, aluminum alloy (2024 T4), stainless steel (AISI 316), carbon fiber, and titanium alloy (grade 5).
The deformation rate of aluminum alloy (2024 T4) is higher than that of the other three materials. Additionally, it has a strong weight-to-strength ratio, making it one of the best materials for creating prosthetic legs. Despite this, it has a weak resistance to corrosion and mediocre machinability. So, using this material for a prosthetic running blade would have a drawback.
The most popular titanium alloy, Ti-6Al-4V, grade 5, is lightweight and has a good strength-to-weight ratio. Along with having great tensile strength and toughness, being corrosion-resistant has an additional benefit. Because of this, this alloy is a great choice for a prosthetic limb. However, titanium alloy is quite expensive.
The least amount of overall deformation occurs in carbon fiber under varying load conditions. Low density, great strength, and durability are requirements for the prosthetic running blade. Excellent mechanical and chemical qualities are offered by carbon fiber.
Carbon fiber appears to be the most profitable option due to its lowest cost per running blade. Titanium alloy grade 5, carbon fiber, AISI 316 stainless steel, and aluminum 2024 T4 alloy cost a total of 78.1, 48.5, 67.6, and 20.9 USD, respectively. It is clear that titanium alloy materials are more expensive than the other materials.