INTRODUCTION
Individuals with disabilities who experience hip joint deterioration often undergo total replacement surgery. However, the artificial joint may require maintenance or parts replacement over time. The preferred method for treating infected total hip replacements is the two-stage exchange. This process involves initial cleaning and potential hardware removal, followed by administering antibiotics at the infection site. The second stage consists of reimplanting the artificial joint after the infection has been eradicated. The time between the two stages can span several months. During this period, antibiotic-infused bone cement is used for the treatment. It can be applied as beads on a string or as a spacer (antibiotic-loaded interim prosthesis). Both methods effectively deliver a concentrated dose of antibiotics to the infected area. However, using a spacer is generally considered superior as it helps prevent soft tissue shortening and maintains proper alignment (Affatato et al., 2003).
Antibiotic-loaded cement spacers are effective for early mobility and concentrated antibiotic treatment. However, there is no standard approach for their use, resulting in the development of individual methods by orthopedic departments. These methods involve creating reproducible spacers using a simple molding form, allowing customization during surgery by adjusting the antibiotic type and amount. Spacer failure is a potential complication due to the limited strength of bone cement (Lewis, 2003). While there are numerous studies on spacers (Meani et al., 2007; Rava et al., 2019), the mechanical strength of polymethyl methacrylate (PMMA) as a spacer material has been examined by only a few authors (Thielen et al., 2009). PMMA is widely used in biomedical applications, particularly in dentistry, since 1937 due to its lightweight, easy processing, polishing, clinical manipulation, low cost, and stability (Fouly et al., 2002). It has been extensively employed as a restorative material. Traditional preparation involves mixing prepolymerized PMMA powder with a liquid-phase monomer called methyl methacrylate (MMA) and placing it in pre-shaped molds (Foul et al., 2021b).
While PMMA has several advantages as a biomedical material, it may not be suitable for all applications. One notable drawback is its surface properties, which make it unsuitable for friction-based applications. PMMA has been found to have poor mechanical properties, including low impact and flexural strengths (Murakami et al., 2013), which can be problematic in certain applications. The improved mechanical properties of PMMA composites, including increased hardness, are particularly relevant when the material is utilized as a spacer and exposed to different types of stress such as shear, friction, and compressive stress. These stresses can have a significant impact on the performance and durability of the spacer, underscoring the importance of enhancing the mechanical properties of PMMA for such applications. These stresses can result in spacer fractures and increased wear rates, causing additional suffering for individuals with disabilities (Alhareb et al., 2015). Sudden fracture is a common issue with PMMA parts such as dentures, owing to their low toughness and brittleness. This not only causes discomfort for patients but also incurs additional healing costs and prolongs recovery time (García-Mansilla et al., 2023).
In the field of biomedical materials, achieving suitable levels of strength, stiffness, and wear resistance is of utmost importance (Puri et al., 2008). To address the limitations of PMMA, researchers are exploring various modifications to enhance its properties. One approach involves chemical modification, which can improve the impact resistance of PMMA through the use of plasma technology and the addition of different agents to enhance cross-linking (Li et al., 1997). Another strategy employed by researchers is the reinforcement of PMMA with different fillers (Karthick et al., 2014). Fillers, such as particles and fibers, can enhance the properties of PMMA composites. According to Kanie et al. (2000), incorporating fillers into polymeric materials is one of the most effective methods for controlling the mechanical properties of polymer composites. In a study by Alhareb et al. (2017), the fracture toughness, impact strength, and hardness of PMMA were investigated after adding different weight fractions of nitrile butadiene rubber (NBR) and ceramic materials such as Al2O3 and yttria-stabilized zirconia (YSZ), along with the addition of a silane agent. The results showed an improvement in all mechanical characteristics, with the optimal mixture consisting of 7.5% NBR, 2.5% Al2O3, and 2.5% YSZ. It has been observed that the incorporation of ceramic fillers in the PMMA composite leads to a notable increase in weight compared to pure PMMA. This weight increase is attributed to the high loading of added materials, which includes ceramic fillers. The weight gain can have implications for the overall weight and bulkiness of the composite material, which may need to be considered in specific applications or design considerations. In a prior study, Asar et al. (2013) investigated the impact of incorporating various metal oxides, including TiO2, ZrO2, and Al2O3, on the mechanical and physical properties of heat-cured PMMA resin. They found that the addition of these metal oxides improved PMMA fracture toughness but also led to negative changes in its physical properties when exposed to human internal fluids. Another research team examined the effects of combining ZrO2/Al2O3 and ZrO2/TiO2 (Alhareb and Ahmad, 2011), obtaining similar results to those reported by Asar et al. (2013).
Researchers have shown increasing interest in the use of natural materials as fillers in composites due to their abundant availability in nature (Fouly et al., 2021a). These materials offer several advantages such as low cost, ease of manufacturing, compatibility with living organisms, and environmentally friendly properties (Mitra, 2014; Fouly et al., 2022a, 2022b). Utilizing natural fillers, such as oil palm empty fruit bunch fiber in cellulose form with a thickness of 0.5 mm, has been found to enhance the flexural strength and modulus of PMMA composites (John et al., 2015). Different research was conducted on incorporating miswak fiber into the PMMA matrix. The study focused on varying the length of miswak fibers (2, 6, and 12 mm) and the weight fractions (3, 6, and 9 wt.%) in the composite material. The incorporation of miswak fiber led to improved physical and mechanical properties of the PMMA composites. This enhancement suggests that the use of miswak fiber as a reinforcement can contribute to the overall performance and strength of the composite material (Salih et al., 2017). Furthermore, the reinforcement of PMMA with miswak and bamboo fibers demonstrated increased compression strength with higher fiber loading fractions. Additionally, researchers explored the use of pomegranate peels as fillers in PMMA resin, observing enhanced mechanical and physical properties in the resulting PMMA composite (Salih et al., 2018).
Coffee, a widely consumed beverage, has gained significant commercial importance in the past century and a half (Daglia et al., 2000). According to the International Coffee Organization, global coffee consumption is immense, with billions of cups being consumed every day. Additionally, the annual production of coffee is estimated to be around 7.5 million metric tons (Ponte, 2002). The production of coffee generates a substantial amount of agricultural waste, accounting for 30–50% of the total weight of coffee produced, depending on the processing method (Oliveira and Franca, 2015). This waste includes coffee pulp and husks, which represent the largest solid by-products of coffee processing. For every ton of coffee fruit, approximately 0.18 tons of husk is produced, constituting approximately 12% of the dry weight of the coffee berry (Adams, 1981). Until recently, these agricultural wastes remained unutilized and their disposal was considered environmentally harmful (Murthy and Naidu, 2012). However, there has been a recent focus on finding alternative uses for coffee industrial waste to mitigate its environmental impact (Mussatto et al., 2011). Despite these efforts, practical solutions for the effective utilization of this waste are yet to be realized. Coffee by-products, particularly coffee husk (CH), contain a significant amount of cellulosic fibers, which can serve as reinforcing fillers in thermoplastic polymers. These fibers possess desirable properties, including low density, good thermal insulation, strong mechanical characteristics, sustainability, and relatively low cost compared to other cellulosic fibers (Faruk et al., 2012).
This study addresses the necessity of developing a new composite material with satisfactory mechanical characteristics for use as a spacer. The authors have opted to utilize PMMA, a commonly used material for spacers in various applications. Recognizing the advantages and potential applications of natural materials, the researchers aim to investigate the mechanical performance of PMMA composites incorporating CH as a raw material. Currently, there is a lack of data regarding the utilization of CH as a filler for polymer composites, particularly without the need for chemical treatment, which can add costs and detract from the goal of utilizing waste material effectively. Therefore, this study presents a complete production process for CH particles without chemical treatment. The mechanical properties of PMMA composites were assessed by evaluating parameters such as hardness, compressive strength, and modulus of elasticity. The evaluation involved using different weight fractions of CH particles in the PMMA matrix. By varying the weight fractions, the researchers aimed to determine the impact of CH particle content on the mechanical characteristics of the composites. Furthermore, a finite element model was developed to simulate the stress on the composite element within the hip joint, considering the obtained mechanical properties from the experiments, and the weight of a human.
MATERIALS AND EXPERIMENTAL WORK
Materials
The self-curing acrylic resin used in this study was sourced from Protechno Famadent S.L.U. in Spain. It is a specialized resin formulated for the purpose of repairing and relining denture plates that are made from acrylic material. The resin is designed to cure without the need for external heat or additional curing agents, making it convenient for dental applications. It is also suitable for hydro-flasking both partial and full dentures. The resin consists of two components: a white powder composed of PMMA, with a density of 1.18 g/cm3, and a colorless liquid monomer containing MMA, with a density of 0.94 g/cm3. As per the manufacturer’s datasheet, the resin exhibits a flexural strength of 65.8 MPa and Young’s modulus of 2263 MPa. To prepare the CHs for experimentation, they were initially ground into smaller pieces using a mortar and pestle. Subsequently, a grain miller was employed to pulverize the pieces at a rotation speed of 200 RPM. The resulting powder was then transferred to a jar within a ball milling machine (Pulverisette 7; Fritsch, Idar-Oberstein, Germany). The machine was set to rotate at 200 RPM, and the milling process lasted for a duration of 8 h. During milling, a cycle of 15 minutes of milling was followed by 15 minutes of rest to prevent excessive heat buildup in the jar.
Fabrication of PMMA composites
For sample preparation, the required amounts of dry PMMA and CH powders were measured based on the desired weight ratios of 0, 2, 4, 6, and 8 wt.%. These powders were then mixed in a ball milling machine for 5 minutes to achieve a uniform dispersion of the CH particles within the PMMA powder. Next, the liquid monomer was added to the mixture at a weight ratio of 5:3.5 (solid to liquid) for all samples. To determine the weight of the solid powder, the weights of the PMMA and CH powders were added together. The mixture of the powders was then manually mixed for a duration of 25 seconds. The mixing process took place at a controlled temperature of 28°C and a relative humidity of 55%. This ensured a uniform distribution of the powders and facilitated the subsequent processing steps. As the mixing progressed, the mixture gradually attained a sticky consistency, similar to dough. Once this stage was reached, typically within 20-30 seconds of mixing, the mixture was placed into cylindrical molds measuring 25 mm × 8 mm. After a curing time of 30 minutes, the samples became fully hardened and were removed from the molds. These procedures adhered to the guidelines and instructions provided by the PMMA manufacturer’s datasheet. In this study, the PMMA–CH composites were produced with different CH weight fractions 0, 2, 4, 6, and 8 wt.%, denoted as PMCH0, PMCH2, PMCH4, PMCH6, and PMCH8, respectively. Figure 1 depicts the production process of the PMMA–CH composite samples.
Characterization and testing
To assess the strength and durability of the PMMA–CH composite, hardness and compression tests were conducted. The hardness of the composite samples was measured using a durometer based on the Shore hardness D index. The durometer had a capacity of 5 ± 0.5 kg and a dwell time of 15 seconds, following the ASTM D2240 standard (Zhao et al., 2015). Six measurements were taken on the surface of each sample, and the average value was calculated, considering the standard errors. The samples were further subjected to compression testing using a computer-controlled servo-hydraulic universal testing machine with a capacity of 30 tons and a strain rate of 1 mm/min. The test results were utilized to determine important mechanical properties of the composite, such as Young’s modulus and the compressive yield strength.
Finite element model
In order to assess the load-bearing capacity of the newly developed PMMA–CH composite when used as a spacer, a finite element model was constructed. Following the approach outlined in a previous study by Ishihara et al., the hip joint was divided into two primary components: the femoral head and the acetabular liner (as depicted in Fig. 2). Using ANSYS software, the spacer was simulated within the hip joint as a replacement for the acetabular liner, as illustrated in Figure 3. The finite element model consisted of a ball connected to the femoral stem, with the spacer material being the newly developed PMMA–CH composite. To establish the boundary conditions for the finite element model, the loading conditions were adopted from a study conducted by Bergmann et al. Their research revealed that hip joints experience a combination of forces in the x, y, and z directions during various types of motion. For instance, in a standing position with a body weight of 100 kg, the maximum resultant forces were determined to be 1540 N, 3480 N, and 70 N in the x, y, and z directions, respectively. In the finite element model, the femoral stem with the ball head was fixed in all directions to represent its attachment to the femur. The interaction between the ball and the PMMA–CH composite spacer was defined as bonded, indicating a strong connection between the two components. The mechanical properties of the PMMA–CH composite used in the model were based on the experimental results obtained in the study. These properties were incorporated into the simulation to accurately represent the behavior of the composite under the specified loading conditions.
RESULTS AND DISCUSSION
As mentioned earlier, the CH powder underwent a two-stage grinding process. The resulting CH powder’s final state is depicted in Figure 2, which presents a scanning electron microscopy image illustrating the morphology of the CH particles. The image reveals that the particles derived from the CH exhibit an irregular, equiaxed shape and possess a rough surface. Furthermore, it is evident that certain particles are considerably smaller in size and tend to cluster together.
The results of the compression test conducted on PMMA composites reinforced with CH are depicted in Figure 4. The findings indicate that an increase in the CH content resulted in enhanced Young’s modulus and compressive yield strength of the PMMA composites. Among the tested compositions, the PMMA composite with 8 wt.% CH demonstrated the highest mechanical strength. The Young’s modulus exhibited a 43.33% increase, while the compressive yield strength improved by 7.56%. This enhancement in compressive yield strength can be attributed to the uniform dispersion of CH particles within the PMMA matrix, enabling efficient transfer and dissipation of the compressive load by the matrix through the CH powder. Furthermore, in the context of compression testing of polymers, the inclusion of filler particles can hinder the propagation of cracks within the matrix as they initiate (Yang et al., 2016). A comparative analysis was performed to investigate the differences in fractographic patterns between the PMMA composite with 8% CH loading (PMCH8) and pure PMMA. Figure 5 depicts the observed variations in the fracture surfaces of the two materials. Notably, the fracture surface of pure PMMA exhibited significant cracks, indicating potential material deterioration and a decrease in mechanical properties. In contrast, the fracture surface of the PMCH8 composite showed fewer cracks and a rougher texture. This increase in surface roughness suggests that the presence of CH particles disrupted the crack propagation path, resulting in improved strength and toughness of the composite material. The fracture surface of pure PMMA exhibited significant crack formations, which can lead to material deterioration and a reduction in mechanical properties. In contrast, the PMCH8 composite exhibited fewer cracks and a rougher surface. The increase in surface roughness indicates that the crack path has been disrupted by the presence of CH particles, implying an enhancement in the composite’s strength.
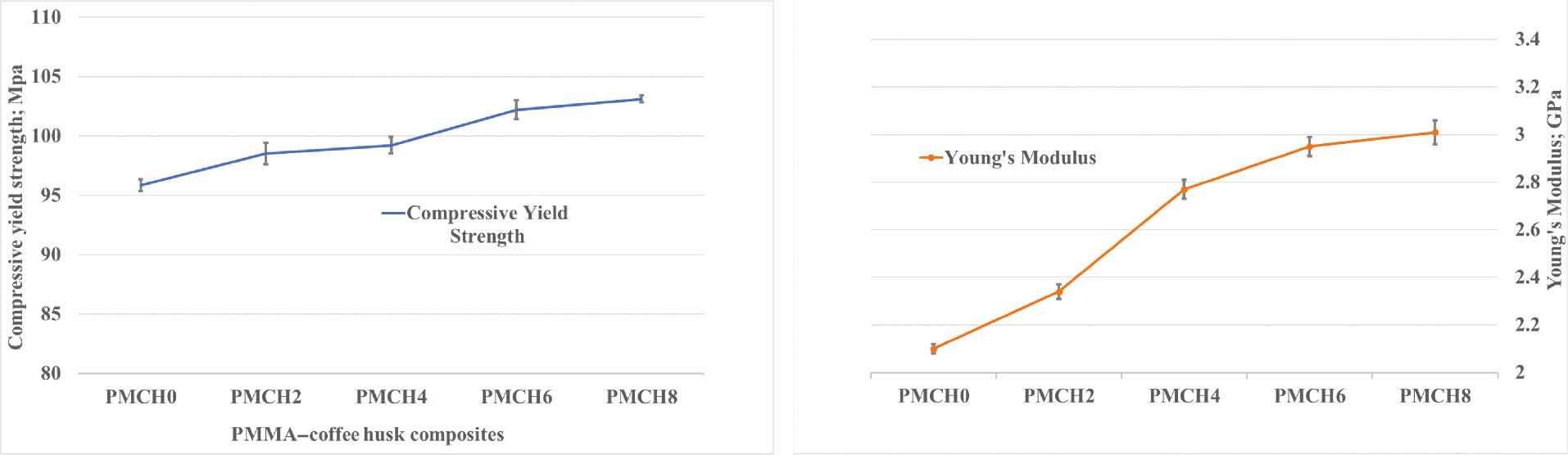
Compressive yield strength and Young’s modulus of PMMA–CH composites. Abbreviation: PMMA–CH, polymethyl methacrylate–coffee husk.
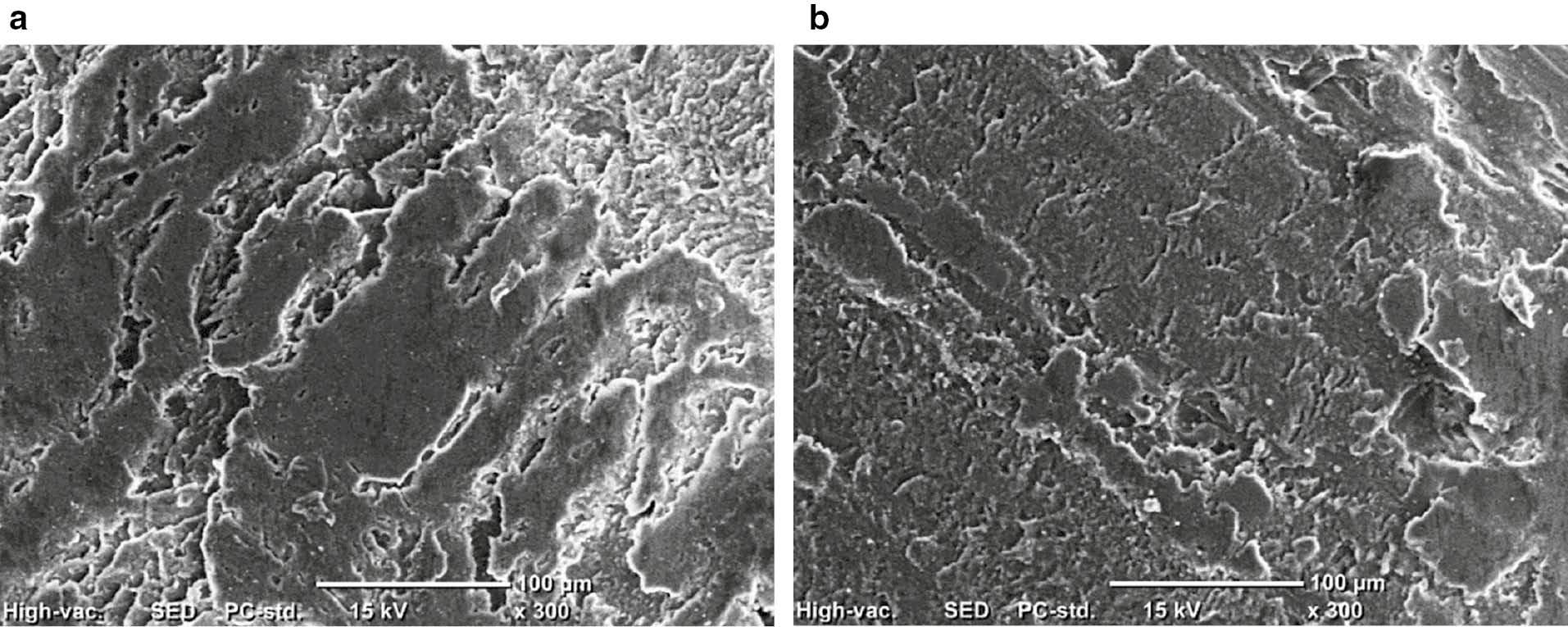
Scanning electron microscopy micrographs of the compressive fractured surface of (a) PMCH0 and (b) PMCH8.
The hardness of the PMMA composite samples was determined using the Shore D index, as depicted in Figure 6. It was observed that as the CH content increased, the hardness of the composites also increased. The highest improvement in hardness, approximately 6%, was observed in the composite with 8 wt.% of CH (PMCH8) compared to pure PMMA. The observed increase in hardness can be attributed to the improved dispersion of CH particles within the PMMA matrix. When the CH particles are well-dispersed and uniformly distributed in the PMMA matrix, they act as reinforcing agents, enhancing the intermolecular bonds and load transfer between the matrix and the filler. This improved dispersion leads to a more efficient load-bearing network, resulting in increased hardness of the composite material. The better dispersion of CH particles also ensures a more uniform stress distribution throughout the material, further contributing to enhanced hardness (Ibrahim et al., 2018). The enhanced dispersion enhances the intermolecular bonds and load transfer between the matrix and the filler, resulting in increased hardness. The higher proportion of CH in the composite also contributes to increased stiffness, which further enhances the hardness. The rise in hardness can be associated with the increased stiffness resulting from the higher proportion of CH.
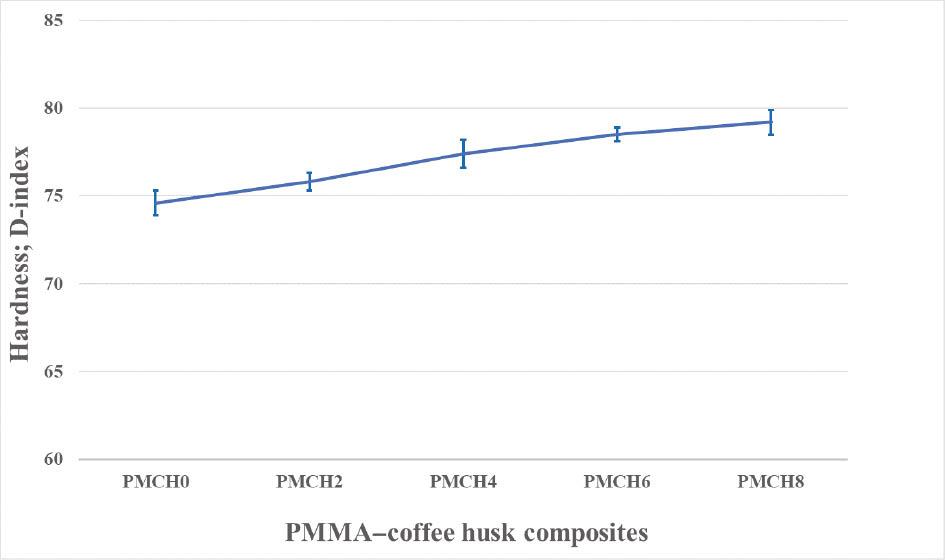
Hardness of PMMA–CH composites. Abbreviation: PMMA–CH, polymethyl methacrylate–coffee husk.
The incorporation of CH particles in the PMMA matrix has been found to enhance its mechanical properties. To assess the load-bearing capability of the composite as a spacer, researchers conducted stress analysis using an ANSYS model of the hip joint incorporating the spacer. The contact stresses on the surface of the spacer under specific conditions were calculated, as illustrated in Figure 7. The highest stress was observed on the inner surface of the spacer in direct contact with the prosthetic head. The von Mises stress and maximum shear stress exhibited slight variations with changes in the CH weight fraction in the PMMA, which corresponded to the improvements in mechanical properties observed in experiments (Fig. 8). An increase in CH content resulted in a decrease in both von Mises stress and maximum shear stress, indicating an improvement in load-carrying capacity Kuminek et al. (2015) and Guo et al. (1997). The highest equivalent stress observed was 32.78 MPa, which is approximately half of the ultimate compressive stress determined in experiments. This suggests that the new PMMA–CH composites are safe for use in spacer production.
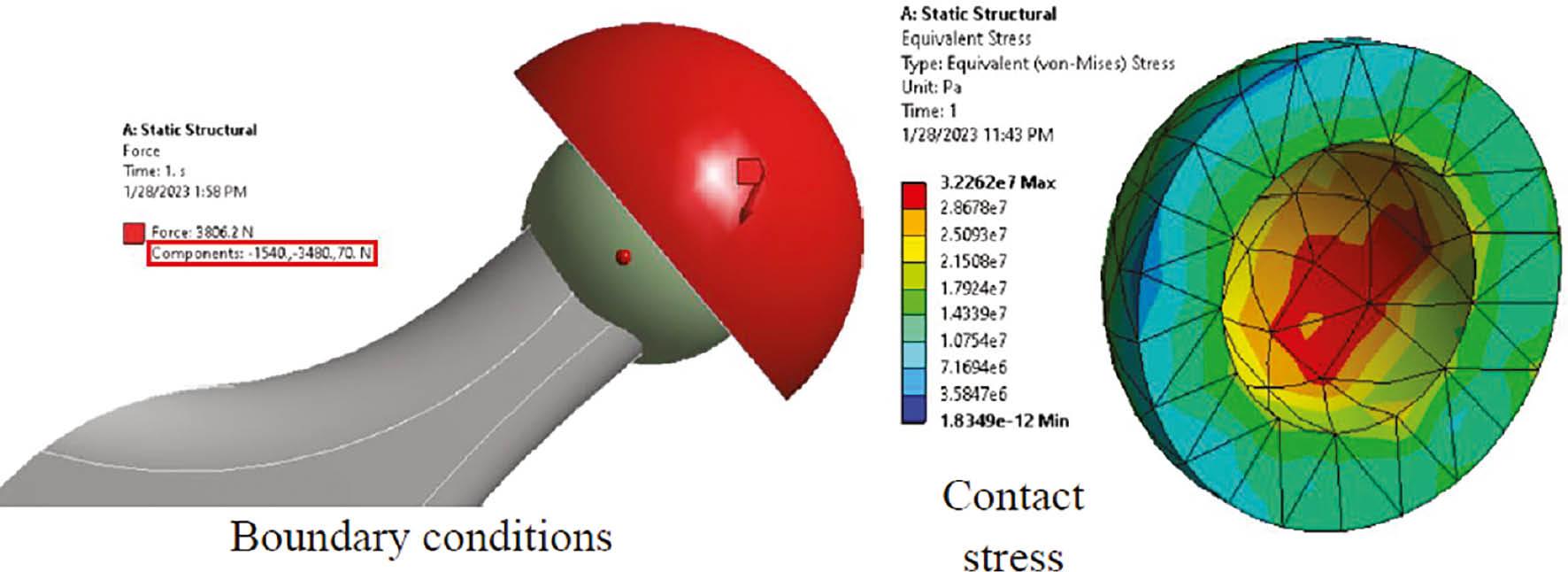
Finite element model with boundary condition, contact stresses for different polymethyl methacrylate– coffee husk composites (Fouly et al., 2023).
CONCLUSIONS
The goal of this investigation was to enhance the mechanical properties of PMMA for use as a spacer in artificial hip joint replacement surgeries. The study involved developing natural CH powder as a reinforcement material and creating PMMA–CH composites with varying weight fractions. The mechanical properties of these composites were evaluated, and an ANSYS model was used to assess the performance of the spacer. The results showed that the addition of CH improved the overall mechanical properties of the composites. Furthermore, the finite element analysis demonstrated that increasing the CH weight fraction reduced the contact stresses on the spacer, indicating an improved load-bearing capability. These findings highlight the potential of using CH as a natural reinforcement to enhance the mechanical properties and performance of PMMA as a spacer material.