INTRODUCTION
As per the report by the Institute for Health Metrics and Evaluation, 57.7 million people are disabled worldwide due to limb amputation. Furthermore, 36.2% of limb amputations were caused by traumatic conditions, 15.7% by road accidents, 11.2% by other transportation accidents, and 10.4% by mechanical impacts (McDonald et al., 2021). In 2015, it was predicted that between 110 million and 190 million individuals living in developing countries have impairments, with more than 90 million of them being adolescents (Sundararaj and Subramaniyan, 2020). Based on these prevalence estimates, approximately 25 million people require prosthetic lower-limb devices globally (Thyssenkrupp, 2018; Abood and Faidh-Allah, 2019; Solis et al., 2021; Talla et al., 2021). Human limb amputation causes enormous changes in the physiological and psychological conditions of a disabled person. There have been several prosthetic devices available to assist disabled persons to reduce dependency on another person. These prosthetic devices are helpful to the disabled in terms of self-dependency, removing social stigma, and participating in social and public events. One of the important segments of life is participation in sports and these events are challenging for disabled persons with lower-limb loss. Participation in sports creates a positive impact on disabled people to achieve their passion and is also beneficial for mental health. Recently, some athletes, such as Oscar Pistorius, the gold medalist in the Olympic track and field, and Mike Schultz, the X Games star, have redefined the sports participation of disabled persons. To deal with this challenging issue, prosthetic running blades have been introduced in the market by some popular companies. The prosthetic running blades have been designed in such a way that they could comfortably fit and give better performance in sports activities such as athletics and marathon running events. The design of prosthetic running blades is a much-debated topic in the research world. Secondly, the selection of materials to manufacture the prosthetic running blade is also a hot topic among researchers. Currently, most of the research works on prosthetic running blades are either focused on design or choice of best materials. The choice of materials becomes an important issue when we have to define the performance of artificial limbs in comparison to natural muscle-based limbs. The question arises as to how and which design and materials could be real replacements. The selection of materials is based on different factors such as mechanical properties (strength, fatigue, ductility, compression, weight, energy loss, etc.) and chemical properties (corrosion, impact from environment, etc.), and also on the cost and availability of materials in particular geographical regions. Because of poverty, high prosthetic pricing, and lack of qualified technicians, many individuals face barriers to these prosthetic devices, particularly for use in sports. It has been observed from the literature that composites, metal, and alloys have been used to manufacture prosthetic running blades (Hagberg et al., 2005; Jayaraman et al., 2019; Krausz and Hargrove, 2019; Parga and Yu, 2019; Villarreal and Gregg, 2019; Damerla et al., 2022; Gomez-Correa and Cruz-Ortiz, 2022). In recent years, some manufacturers are enabling sports persons to engage in their preferred sports events, by using novel advanced materials and utilizing cutting-edge technologies (Jönsson et al., 2011; Mauroy et al., 2012; Devaraj et al., 2020; DeVillez et al., 2022). Patients can participate in more demanding recreational activities such as jogging thanks to specialized prosthetics known as prosthetic improvements. These artificial limbs are being featured more frequently at important athletic events such as the Olympics. According to some studies, the energy used by the legs is only 25% of what a leg in good physical condition would consume. High-performance prosthetic running legs made of carbon fiber perform better than their metal counterparts in many ways. The current running blades made of carbon fiber, sold by Ossur (Reykjavík, Iceland), have the best performance available. These blades are thinner and better able to hold strain energy. Carbon fiber is used to make the blades themselves, which are light. Carbon fiber is a tough substance that is five times stronger and stiffer than steel. The blade is created by layering tightly twisted strands of carbon fiber that have been put on top of one another to create a continuous layer. Energy-storing and -returning feet have been created in response to the high demands of athletic competition and the desire of people with lower-limb amputations to participate in sports (Gallagher and MacLachlan, 2004). To help with forward propulsion, these feet might store energy during stance and release it to the wearer in late stance. However, there has not been much research done on their dynamic properties (natural frequencies, mode shapes, and damping) while they are running. What matters more is whether an athlete’s performance in a Paralympic sport may be significantly impacted by the length of a blade. Many blade makers assert that no two pairs of blades will be the same because no two athletes who use the same blades are the same. Based on their various natural heights, each athlete’s ideal and most natural running blade length is determined. The International Paralympic Committee (IPC) has acknowledged that more research is necessary to pinpoint the precise effects of various running blade types in sports, though. Blades can be fitted with running spikes, much like regular running shoes, to improve their traction on the ground. These are frequently applied by hand and may be difficult to attach to the svelte carbon fiber blade. Nike (Beaverton, OR, USA) provided Oscar Pistorius with custom “spike pads” that are attached to the underside of the blade as his spikes. The design of running blades, in particular, must account for the runner’s weight and impact level while still providing adequate traction (Grimmer et al., 2014; Liu et al., 2017; Chereshnev and Kertész-Farkas, 2018; Frossard et al., 2019; Petrone et al., 2020; Rankin et al., 2020; Emonds and Mombaur, 2021; Aftab and Ahmed, 2022; Murabayashi et al., 2022; Shim et al., 2022). Rahman et al. (2014) and others revealed that modern materials can lessen the strain on a running blade’s body and also require fewer carbon fiber layers. They were able to lighten the body’s overall composition thanks to this new design. Shastry et al. (2021) mentioned that because the new designs significantly provide enough torque and force, disabled people can easily and actively use prosthetic legs. According to a report, the cost of prosthetic legs is the main source of worry, but new materials should be more affordable for those with money constraints. Laminate composite materials were studied by Ouarhim et al. (2021). They investigated glass fiber and polyester woven and chopped strand mats. The researchers concluded that material selection and design affect the relaxation dynamics of running blades.
The majority of studies have either concentrated on the design of prosthetic running blades or the materials used. Al-Waily and Mechi (2021) studied the stress and deformation in the running blade. In their review research work, Safari (2020) has extensively discussed the design aspect of prosthetic legs and limbs. They stated that advanced types of running blades are being developed with the help of new material technology. Migliore et al. (2020) investigated the biomechanical impact on the prosthetic sockets of sprinters who won gold at the Paralympics. The mechanical properties of the socket used for below-knee prosthetics have been improved through research by some authors. Sockets were made from composite materials (Kevlar), and stress and deformation were researched. Jweeg et al. (2019) specifically mentioned the use of the steel grades AISI 4130 and the aluminum alloys 6061 and 7075 for knee joints (Kadhim et al., 2018). It is common knowledge that different activities, such as running, walking, or ascending and descending stairs, require different prosthetic devices. Tryggvason et al. (2017) investigated the idea of determining ankle stiffness characteristics using the finite element method. Furthermore, Colombo et al. (2016) investigated the limb socket to enhance its functionality. Using finite element simulation, they investigated pressure distribution. A good prosthetic design should have a number of key elements, including comfort, less energy loss, and realistic flex close to the human leg muscle. Noroozi et al. (2013) examined the natural frequencies, damping, and mode shapes of artificial running blades. It is important to note that modern materials and design techniques would fundamentally alter how prosthetics are currently created (Powell et al., 2020). By reviewing the literature, it can be summarized that static performance of prosthetic running blades made from different materials still need evaluation and analysis.
The static behavior of running blades is the very first step in design and development. The analysis of static and structural performance is required under several physical conditions. According to the literature, not much research has been done on the impact of materials on the performance of prosthetic running blades when taking into account loads from standing, walking, and running. Especially, some advanced materials such as titanium alloy, carbon fiber, stainless steel alloy, and aluminum alloy (2024 T4) have been used in prosthetic designs. Understanding the functionality of prosthetic legs made of titanium alloy, carbon fiber, stainless steel alloy, and aluminum alloy is our goal. In this study, we carried out the three-dimensional finite element analysis of prosthetic running blades under various static loads. Additionally, a comparison of various materials will be beneficial for structural analysis. Disability-related aspirations in sports and athletics will be aided by any small developments in this area.
MATERIALS AND METHODS
In this study, we employed four common materials for running blades: titanium alloy, carbon fiber, stainless steel, and aluminum alloy (2024 T4). We have adopted a running blade’s geometrical design and dimensions from a commercial product. A three-dimensional Computer Aided Design (CAD) model was created using a great deal of research into the running blade’s design. We have used a design that is close to the design of a commercially available running blade by Levitate Technology ApS (Roskilde, Denmark). The SpaceClaim software (Ansys Inc., Canonsburg, PA, USA) was used to create the geometry. Additionally, using Ansys Mechanical software, meshing and structural analysis have been done. The top of the running blade assembly has received the force in this numerical work. We have taken into account three different postures for athletes, including standing, walking, and running. Table 1 shows the force associated with each of the three postures. The force was applied vertically to the running blades for static behavior analysis. Four different materials were subjected to numerical analysis for this study. We looked at how running blades behave mechanically when users are standing, walking, and running in various scenarios. Table 2 lists the mechanical characteristics of various materials. The running blade behavior under various test loads was simulated using the Ansys Finite Element module. The running blade’s style was influenced by the running blade that is readily available in stores. Figure 1(a) illustrates the running blade’s dimensions, and Figure 1(b) shows different parts of the running blade. The meshing details have been shown in Figure 2. By using a grid independence test, we predetermined the number of elements in this numerical model. Table 3 illustrates the specific mesh size and element count. To determine the appropriateness of the number of elements, we used the total deformation at the running blade’s midplane as the criterion. We concluded that mesh size 66,071 is the best for delivering respectable results based on the total deformation results. Further, we validated our finite element model with previous work by Ouarhim et al. (2021). Figure 3 shows the comparison of total deformation from our current model and the work of Ouarhim et al. We found that our results are under the limit of 2.5% of variations.
Material properties.
No. | Property | Materials Aluminum (2024-T4) | Steel (AISI-316 stainless steel) | Carbon fiber | Titanium alloy [Titanium Ti-6Al-4V (grade 5), annealed] |
---|---|---|---|---|---|
1 | Modulus of elasticity (GPa) | 73 | 193 | 230 | 96 |
2 | Poisson’s ratio | 0.33 | 0.31 | 0.2 | 0.36 |
3 | Yield strength (MPa) | 324 | 207 | 2500 | 930 |
4 | Tensile strength ultimate (MPa) | 469 | 586 | 3590 | 1070 |
5 | Comp. strength (MPa) | — | 207 | — | 930 |
6 | Density (kg/m3) | 2780 | 7750 | 1750 | 4620 |
7 | Melting point (C) | 638 | 1400 | 3652 | 1660 |
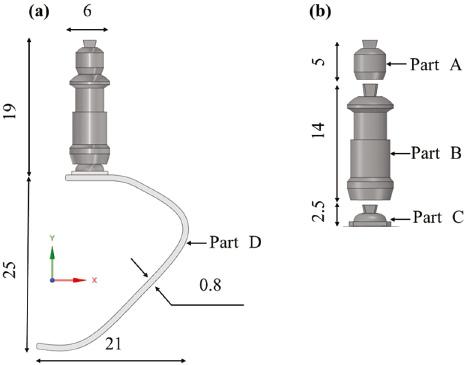
The schematic diagram of prosthetic running blade. (a) Dimensions of the prosthetic running blade (in mm); (b) different parts of the prosthetic.
RESULTS AND DISCUSSIONS
In this work, we studied the effect of static load on a prosthetic running blade. The static force was applied on the top surface of the running blade. As mentioned earlier, we used three different conditions to analyze the impact of static load. These three conditions are standing condition (700 N), walking condition (1400 N), and running condition (2100 N). Figures 3–6 show total deformation in the running blade while the force was 2100 N at that instant. Figure 3 illustrates the total deformation in the running blade made of aluminum alloy. About 4.3-4.5% copper, 0.5-0.6% manganese, 1.3-1.5% magnesium, and less than 0.5% of silicon, zinc, nickel, chromium, lead, and bismuth constitute the makeup of aluminum alloy. It is used in situations where a high strength-to-weight ratio and strong fatigue resistance are required. It has a fair amount of machinability and can also be joined through friction welding. Not to mention that in each case of simulation, parts A, B, and C have been selected as Al alloy, and the part D (running blade) has been chosen as different materials in each case. It can be observed in Figure 3 that maximum deformation occurs in the middle of a curved segment of the running blade. Similarly, if we compare Figure 4 with the previous one, we say that the titanium alloy has less deformation. Titanium alloy exhibits better mechanical properties as compared to aluminum alloy. The titanium alloy has higher tensile strength and toughness. However, the high cost of titanium alloy and processing are major drawbacks to using it in the running blade. We investigated carbon fiber for running blades. The total deformation contours are illustrated in Figure 5.
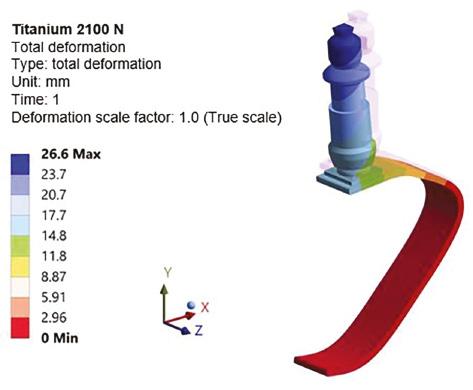
The contours of the total deformation in the titanium alloy running blade at 2100 N static load.
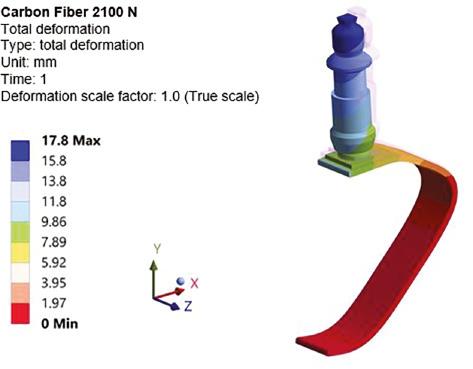
The contours of the total deformation in the carbon fiber running blade at 2100 N static load.
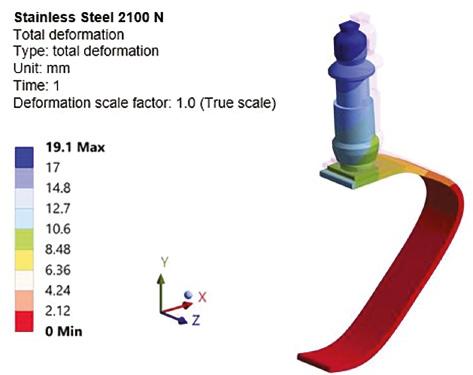
The contours of the total deformation in the stainless steel alloy running blade at 2100 N static load.
Carbon fibers possess excellent mechanical properties, which are very critical for manufacturing running blades. It poses excellent tensile properties. In addition to this, the low density of carbon fiber has added the advantage of making a lighter running blade. Another benefit of carbon fiber-based running blades is that it can have excellent creep resistance. However, it poses some challenges in manufacturing the running blade. Further, the total deformation in the stainless steel running blade is shown in Figure 6. The carbon fiber material excels as compared to stainless steel. However, stainless steel has some specific advantages and disadvantages too.
The plot of equivalent stress, maximum principal stress, and shear stress during static load has been depicted in Figure 7. It is noted here that equivalent stress (von Mises) is maximum in the aluminum alloy and titanium alloy as compared to the other two materials. The value of equivalent stress varies from 1500 MPa to 2500 MPa. The von Mises stress is helpful to understand the yielding of prosthetic materials under uniaxial loading. Hence, the value for each equivalent stress is quite on the higher side, and we expect that all four materials would perform well on the yielding parameter. Secondly, we can also observe the maximum principal shear stress plot for different materials. This parameter is helpful to understand the fracture resistance capability of the prosthetic running blade. Thus, it can be said that if a prosthetic running blade comes under multiaxial stress conditions, then fracture happens at the location where maximum principal stress exceeds the local strength of the blade at any point. As it is evident, the maximum principal stress is more than enough for all four materials. Further, shear stress can be also evaluated from the plot for all four materials. It can be seen here that the shear stress range falls under 450-700 MPa for all cases of materials that are under the acceptable limit. Moreover, we have presented more details of stress generation in Figures 8 and 9 at different static load conditions. Figure 8 illustrates the plot of elastic strain (von Mises) at different reaction forces on the running blade. The trend of the results seems linear for the four materials. In addition to this, Figure 9 shows the comparison of shear stress with different reaction forces on the running blade. In this plot, we can observe that the relationship among all four materials is linear. The physical activity of athletics causes shear effect on running blade in a certain condition. Hence, a prosthetic running blade must be evaluated for any specific design.
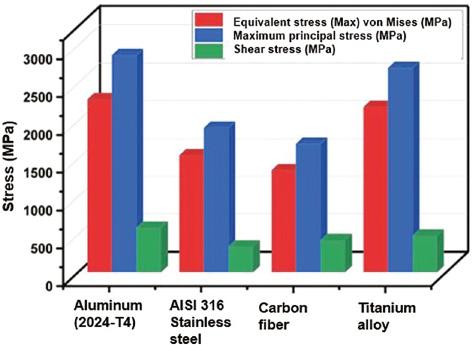
Plot of equivalent stress, maximum principal stress, and shear stress for different materials.
Figure 10 compares the values of normal elastic strain and normal stress for four selected materials for a prosthetic leg. It can be observed here that normal elastic strain is minimum for stainless steel and carbon fiber. In contrast to this situation, normal elastic strain values are higher for aluminum alloy and titanium alloys. The normal elastic strain represents the elongation of the running blade under normal stress. Here, it can be observed that carbon fiber and stainless steel perform better in terms of normal strain. While titanium alloy and aluminum alloy have higher strain values. Moreover, normal stress is also shown for each material during the static load conditions in Figure 10. Subsequently, we studied the strain energy and its relationship with different reaction forces, which is shown in Figure 11. The strain energy has a non-linear trend as it is observed from the plot. The values of strain energy are lower for the carbon fiber material as compared to the other three materials. This plot shows a detailed overview of the strain energy relationship concerning reaction force.
CONCLUSIONS
Lower-limb amputation for humans is a big challenge for a disabled person to live and integrate socially. A disabled person who has lost a leg can be rehabilitated easily by using prosthetic legs. One of the major challenges associated with them is to participate in sports activity. Humans are emotionally connected with sports and any participation in sports activity enhances mental peace. Thus, it is an important aspect and requirement of prosthetic running blades that could help disabled persons to participate in sports activity especially a marathon, outdoor activities, etc. Secondly, the prosthetic running blades need to be efficient in terms of performance and lower cost, so that most disabled persons can afford them.
In this work, we studied the performance of prosthetic running blades made of four different materials, namely, aluminum alloy, stainless steel, titanium alloy, and carbon fiber. We used the numerical technique finite element model to analyze the impact of loads on the running blade. A detailed analysis has been made based on the simulated results.
It was discovered that the running blade’s curved segment’s center is where the most deformation takes place.
The deformation rate of aluminum alloy (2024 T4) is higher than that of the other three materials. Additionally, it has a strong weight-to-strength ratio, making it one of the best materials for creating prosthetic legs.
The mechanical qualities of titanium alloy are superior to those of aluminum alloy. The tensile strength and toughness of the titanium alloy are greater. However, a significant barrier to adopting titanium alloy in the running blade is its high cost of production.
Excellent mechanical qualities, which are crucial for producing running blades, are offered by carbon fibers. It has exceptional tensile qualities.
In addition, carbon fiber’s low density provides the added benefit of making running blades lighter. Running blades made of carbon fiber can also offer great creep resistance. It does, however, provide significant production difficulties for the running blade.